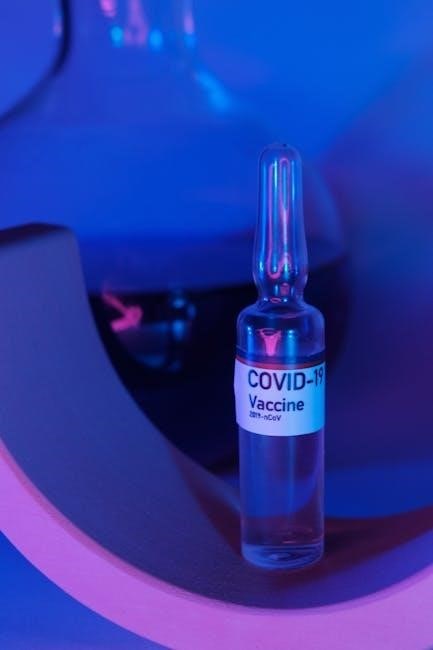
Injection Molding Defects: Causes and Remedies
Injection molding defects arise during the manufacturing process‚ stemming from mold issues or improper processing. Identifying causes and implementing effective remedies is crucial for producing quality parts and optimizing the injection molding operation.
Injection molding‚ a widely used manufacturing process‚ is susceptible to various defects that can compromise the quality and functionality of the final product. These imperfections can arise from a multitude of factors‚ including material properties‚ mold design‚ processing parameters‚ and equipment condition. Understanding the causes of these defects and implementing appropriate remedies are essential for achieving optimal production efficiency and minimizing material waste.
This section provides an overview of common injection molding defects‚ exploring their origins and offering practical solutions for prevention and correction. By identifying the root causes of these issues‚ manufacturers can fine-tune their processes‚ optimize mold designs‚ and select appropriate materials to ensure consistent production of high-quality parts. Effective troubleshooting and implementation of corrective measures are critical for maintaining product integrity and meeting customer expectations. This guide serves as a valuable resource for addressing and resolving injection molding defects‚ contributing to improved manufacturing outcomes.
Common Injection Molding Defects
Numerous defects can arise during injection molding‚ impacting product quality. These include flow lines‚ sink marks‚ weld lines‚ and short shots. Understanding these common issues enables effective remedies and optimized processes.
Flow Lines: Causes and Remedies
Flow lines‚ often visible as streaks or patterns on the molded part’s surface‚ are a common injection molding defect. They occur when molten plastic cools at varying rates as it flows into the mold cavity. Several causes contribute to this issue‚ including slow injection speed‚ inadequate melt temperature‚ and variations in material viscosity.
To remedy flow lines‚ several adjustments can be implemented. Increasing the injection speed and melt temperature ensures a more consistent flow of plastic. Optimizing the mold temperature and gate design promotes uniform cooling. Proper venting of the mold cavity is essential to remove trapped gases that can hinder plastic flow. Additionally‚ material selection plays a crucial role‚ with certain polymers exhibiting better flow characteristics than others. Careful consideration of these factors can significantly reduce or eliminate flow lines‚ resulting in improved part aesthetics and structural integrity. Moldflow simulation can improve the flow.
Sink Marks: Causes and Remedies
Sink marks are depressions or indentations that appear on the surface of an injection molded part‚ typically in thicker areas. These defects are caused by volumetric shrinkage of the plastic material during cooling. When the outer surface of the part cools and solidifies faster than the inner core‚ the shrinking core pulls the surface inward‚ creating a sink mark.
Several factors contribute to sink marks‚ including thick part designs‚ insufficient cooling time‚ low packing pressure‚ and high melt temperatures. To remedy sink marks‚ adjustments can be made to the mold design and process parameters. Reducing the wall thickness in problematic areas promotes more uniform cooling. Increasing the cooling time allows the core to solidify adequately. Optimizing the packing pressure compensates for material shrinkage. Lowering the melt temperature reduces the overall shrinkage rate. Gate location can also impact sink marks.
Weld Lines: Causes and Remedies
Weld lines‚ also known as knit lines‚ are visible lines or weak points on the surface of an injection molded part where two or more flow fronts of molten plastic meet. These defects occur when the converging plastic streams cool down before completely merging‚ resulting in incomplete bonding. Weld lines can compromise the structural integrity and aesthetic appeal of the part.
Several factors contribute to weld lines‚ including low melt temperature‚ slow injection speed‚ complex part geometry‚ and insufficient venting. To remedy weld lines‚ increasing the melt temperature enhances the flowability of the plastic‚ promoting better fusion. Optimizing the injection speed ensures that the plastic reaches the meeting point before cooling. Improving the mold design to ensure a more uniform flow of plastic can significantly reduce weld lines. Adjusting the temperature of the mold and selecting suitable materials enhances the chances of molten plastic fronts merging successfully.
Short Shots: Causes and Remedies
A short shot is an injection molding defect where the molten plastic fails to completely fill the mold cavity‚ resulting in an incomplete part. This occurs when there isn’t enough material to fill the mold‚ or when the plastic solidifies before reaching all areas. Short shots lead to unacceptable parts that don’t meet dimensional requirements.
Several factors can cause short shots‚ including insufficient material volume‚ low injection pressure‚ inadequate venting‚ and obstructions in the flow path. To remedy short shots‚ ensure an adequate amount of molten plastic is injected into the mold. Increasing the injection pressure and speed can help the plastic reach all areas. Proper venting allows air to escape‚ preventing air traps that hinder plastic flow. Optimizing gate locations and runner sizes reduces flow restrictions and minimizes pressure drop. Raising the mold temperature can also improve plastic flow.
Flash: Causes and Remedies
Flash‚ a common injection molding defect‚ appears as excess material extending beyond the intended part edges. This occurs when molten plastic escapes from the mold cavity‚ typically at the parting line. The thin‚ unwanted plastic layer can compromise the part’s appearance and functionality.
Several factors contribute to flash‚ including excessive injection pressure‚ insufficient clamping force‚ high melt temperatures‚ and improper mold alignment. To remedy flash‚ reduce the injection pressure to prevent plastic from being forced into gaps. Increase the clamping force to ensure the mold halves are tightly sealed. Lower the melt temperature to reduce the plastic’s fluidity. Inspect and maintain the mold to ensure proper alignment and sealing. Consider adjusting the parting line design to minimize potential escape routes for the molten plastic. Proper mold maintenance and parameter adjustments are crucial for preventing flash.
Warpage: Causes and Remedies
Warpage is a distortion defect where the molded part changes shape from its intended design. Uneven shrinkage during cooling is the primary cause. Different sections of the part cool at varying rates‚ leading to internal stresses that result in bending or twisting.
Several factors contribute to warpage‚ including non-uniform wall thickness‚ improper cooling channel design‚ excessive mold temperature‚ and material selection. To remedy warpage‚ ensure consistent wall thickness throughout the part design to promote uniform cooling. Optimize the cooling channel layout to provide even temperature distribution. Reduce mold temperature to minimize shrinkage variations. Consider using materials with lower shrinkage rates or incorporating reinforcing fillers. Adjust injection parameters‚ such as pressure and speed‚ to minimize internal stresses. Proper mold design and careful control of the cooling process are essential for preventing warpage.
Burn Marks: Causes and Remedies
Burn marks appear as black or dark discoloration on the surface of molded parts. The primary cause is trapped air or gas overheating during the injection molding process. Excessive injection speed‚ high melt temperature‚ and inadequate venting can lead to this defect.
To remedy burn marks‚ optimize venting to allow gases to escape the mold cavity. Reduce injection speed and melt temperature to prevent overheating. Ensure proper mold design with sufficient gate size and runner system to facilitate smooth material flow; Check for any obstructions in the mold that may trap air. Adjust clamp force if needed. Consider using materials with better thermal stability. Proper process control and mold maintenance are crucial for preventing burn marks and ensuring high-quality molded parts. Regular cleaning of the mold can help remove residue that contributes to the problem.
Material Related Defects
Material-related defects in injection molding stem from issues like contamination or degradation. These defects impact the final product’s appearance and performance. Addressing these causes with appropriate remedies ensures quality;
Discoloration: Causes and Remedies
Discoloration‚ a color defect‚ manifests as a change from the original material color in molded parts. Common causes include material degradation due to excessive injection speed‚ prolonged residence time‚ or high melt temperature. Improper screw or runner system designs exacerbate material degradation‚ leading to discoloration.
To find remedies‚ consider the following. First‚ optimize injection parameters like speed‚ temperature‚ and pressure. Reducing back pressure can also help. Evaluate the screw and runner system design for improvements that minimize material stagnation. Proper cleaning of the mold and equipment is also essential.
Material contamination is another potential cause of discoloration. Ensure the material is stored and handled correctly to prevent contamination. Regular maintenance of the molding machine and mold can prevent discoloration problems. Always verify the material compatibility with the intended application. By addressing these factors‚ discoloration can be effectively mitigated‚ ensuring consistent product quality.
Process Parameter Optimization
Optimizing process parameters‚ such as temperature‚ pressure‚ and speed‚ is crucial for reducing defects. Adjustments to these parameters can prevent issues and improve the overall quality of injection molded parts.
Adjusting Injection Speed and Pressure
Injection speed and pressure are critical parameters in injection molding‚ significantly impacting the quality of the final product. Adjusting these parameters can help mitigate common defects. Too slow injection speed may cause flow lines or short shots‚ while excessively high speeds can lead to burn marks or jetting.
Optimizing injection pressure ensures the mold cavity is filled adequately. Insufficient pressure results in short shots and sink marks‚ while too much pressure can cause flash. Finding the right balance is essential for consistent and defect-free parts.
Material viscosity‚ mold temperature‚ and part geometry influence optimal settings. Monitoring and adjusting these parameters during the injection molding process is crucial for achieving desired results and minimizing defects. Proper adjustment enhances the merging of molten plastic fronts.
Mold Design Considerations
Mold design plays a vital role in preventing injection molding defects. Proper design ensures uniform plastic flow‚ adequate venting‚ and efficient cooling‚ all crucial for high-quality parts.
Gate Design and its Impact on Defects
Gate design significantly impacts the quality of injection molded parts. The size‚ type‚ and location of the gate influence plastic flow‚ pressure distribution‚ and cooling rates‚ all affecting the likelihood of defects.
A poorly designed gate can cause several problems; Small gates restrict flow‚ leading to high shear stress and potential material degradation‚ causing issues like flow lines or burn marks. Improper location can result in uneven filling‚ leading to weld lines‚ air traps‚ or warpage.
Optimizing gate design involves considering part geometry‚ material properties‚ and processing parameters. Moldflow simulation helps analyze flow patterns and identify potential issues. Larger gates reduce shear but increase vestige. Balancing these factors is crucial for minimizing defects and achieving consistent part quality in injection molding.